Introduction
|
The Alfa Laval SaniJet 20 UltraPure is a rotary jet head tank cleaning machine for hygienic environments. Built to clean tanks with capacities from 5-30 m3 it combines pressure and flow to create high-impact cleaning jets that rotate in a repeatable and reliable 360-degree cleaning pattern. |
The SaniJet 20 UltraPure minimizes the consumption of water and cleaning media. Easy to customize to meet customer requirements, it allows companies to spend less time cleaning and more time producing. |
Alfa Laval UltraPure equipment is designed and configured to meet the high demands of the biotech and pharmaceutical industry. Special attention is given to documentation, material and surface finish, in compliance with current Good Manufacturing Practices (cGMP) and other guidance for this industry. |
|
Application
|
The Alfa Laval SaniJet 20 UltraPure is designed for the removal of the toughest residues from hygienic tanks across a broad range of industries, such as the pharmaceutical and personal care industries. |
|
Benefits
|
- 60% faster cleaning = more time for production
- Saves up to 70% of your cleaning cost
- High-impact cleaning in a 360° repeatable cleaning pattern
- Cleaning process can be validated using Alfa Laval Rotacheck
- Alfa Laval Q-doc documentation package for full traceability of product-contacted parts and smooth qualification and validation processes
|
|
Standard Design
|
The choice of nozzle diameters can optimize jet impact length and flow rate at the desired pressure. |
|
Working principle
|
The high-impact jet stream from the Alfa Laval SaniJet 20 UltraPure rotary jet head covers the entire surface of the tank interior in a successively denser pattern. This achieves a powerful mechanical impact with a low volume of water and cleaning media. |
The flow of the cleaning fluid makes the nozzles perform a geared rotation around the vertical and horizontal axes. In the first cycle, the nozzles lay out a course pattern on the tank surface. The subsequent cycles gradually make the pattern denser until at full cleaning pattern is reached. Once the full cleaning pattern is reached, the machine will start over again and continue to perform the next full cleaning pattern. |
|
Cleaning Pattern
|
Example - 2xØ3.8LS |
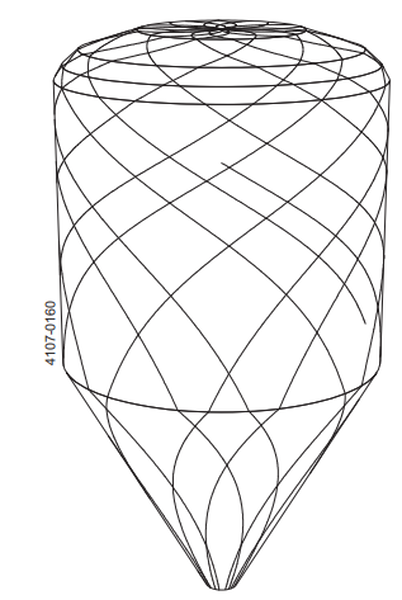 |
|
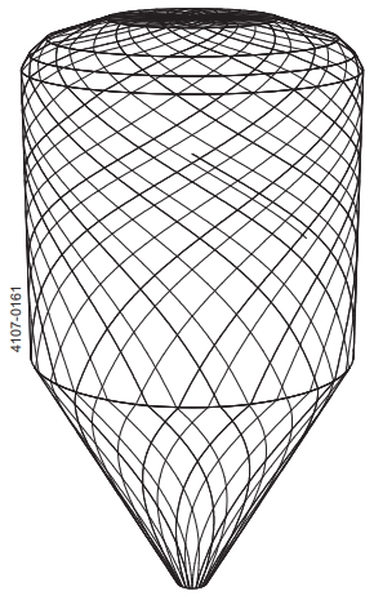 |
|
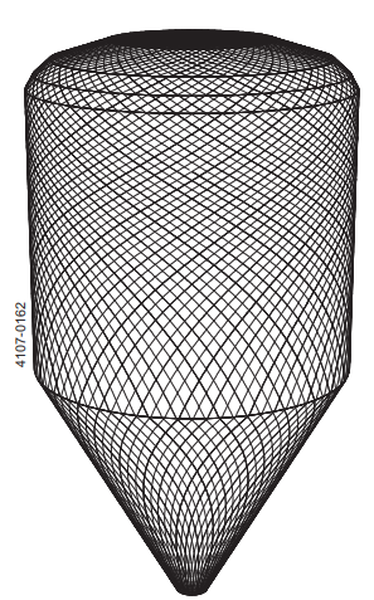 |
0.8 min. |
|
2.3 min. |
|
6.0 min. |
|
|
Certificates
|
Q-doc, Q-doc incl. FAT & SAT and ATEX. |
 |
|
TECHNICAL DATA
|
|
Lubricant |
|
Machine: |
Self-lubricating with the cleaning fluid |
Air motor: |
Can operate non-lubricated |
|
|
Surface finish |
|
Product contact parts: |
3Ra 0.5 µm |
|
|
Impact throw length |
|
Impact throw length: |
1.5 - 4 m |
|
|
Tank opening |
|
Min. tank opening: |
4" Clamp w. rotacheck
3" Clamp - rotacheck N/A |
|
|
Pressure |
|
CIP media working pressure: |
3 - 13 bar |
CIP media recommended pressure: |
5 - 8 bar |
|
|
Air driven. Air quality |
|
Clean, filtered max.: |
40 µm |
Dry, dew point max.: |
5 °C Non-lubricated possible |
Air supply pressure: |
Max. 7 bar |
Free air consumption: |
Max. 2 l/sec. (8 m3 /h) |
|
|
|
|
Adjustable speed: |
5 - 16 RPM |
Cleaning time: |
3 - 10 min |
|
|
Caution |
|
Avoid hydraulic shock, hard and abrasive particles in the cleaning liquid, as this can cause increased wear and/or damage of internal mechanisms. In general, a filter in the supply line is recommended. Do not use for gas evacuation or air dispersion. For steaming we refer to the manual. |
|
|
Qualification Documentation |
Designed for the BioPharm and Personal Care industry for qualification of hygienic Tank Cleaning Machines. Developed in according to the ISPEV-model and GDP, Good Documentation Practice, and includes: RS (Requirement Specification); DS (Design Specification incl. Traceability Matrix);FAT (Factory Acceptance Test incl. IQ & OQ); 3.1 and USP Class VI Certificates;FDA Declaration of Conformity; TSE Declaration; QC Declaration ofConformity; SAT (Site Acceptance Test Protocol incl. IQ & OQ) for End-User Execution. |
|
Documentation specification |
|
|
Q-doc |
Equipment Documentation includes:
- EN 1935/2004 DoC
- EN 10204 type 3.1 inspection Certificate and DoC
- FDA DoC
- GMP EC 2023/2006 DoC
- EU 10/2011 DoC
- ADI DoC
- QC DoC
- USP Class VI certificate
|
|
|
|
Q-doc +
FAT-SAT |
Qualification Documentation includes:
- Q-doc
- RS, Requirement Specification
- DS, Design Specification incl. Traceability Matrix
- FAT, Factory Acceptance Test incl. IQ and OQ
- SAT, Site Acceptance Test protocol incl. IQ and OQ for End-User Execution
|
|
|
|
ATEX |
ATEX approved machine for use in explosive atmospheres.
Media/Air driven:
Catagory 1 for installation in zone 0/20 in accordance with Directive 2014/34/EU
- II 1G Ex h IIC 85 °C ...175 °C Ga
- II 1D Exh IIIC T85 °C ...T140 °C Da
|
Air motor unit:
Catagory 2 for installation in zone 1/21 in accordance with Directive 2014/34/EU
- II 2G Ex h IIC T4 Ga
- II 1D Ex h IIIC T135 °C Da
|
|
|
|
|
Flow Rate
|
|
Cleaning Time, Complete Pattern, Media driven
|
|
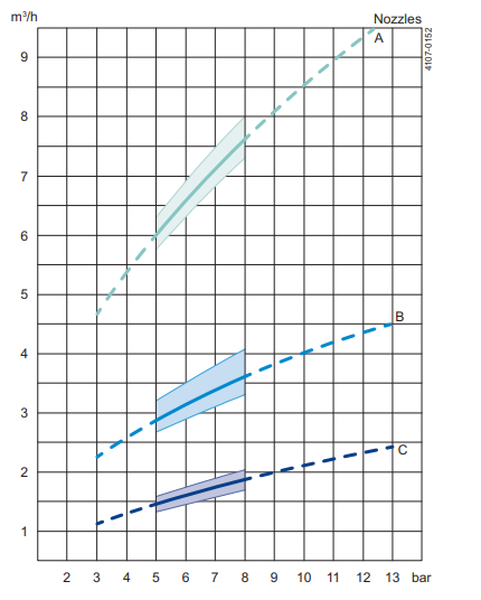 |
|
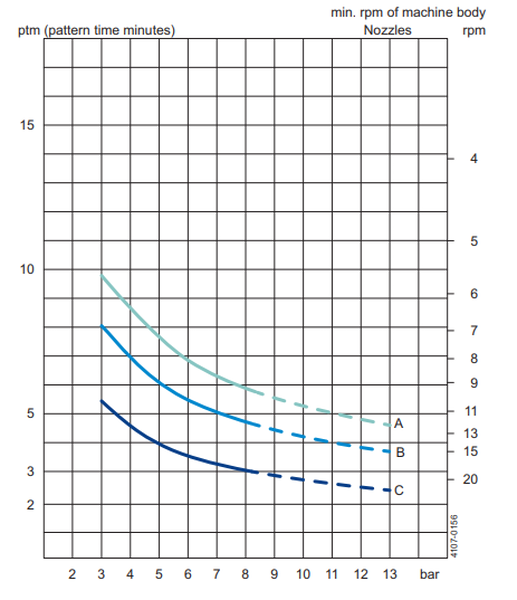 |
|
Inlet pressure |
|
Inlet pressure |
Recommended operating pressure 5-8 bar |
|
|
|
A = 4 x Ø4.2 mm
B = 2 x Ø3.8 mm LS
C = 2 x Ø2.0 mm |
|
A = 4 x Ø4.2 mm
B = 2 x Ø3.8 mm LS
C = 2 x Ø2.0 mm |
|
|
Impact Throw Length, Air Driven
|
|
Impact Throw Length, Media Driven
|
|
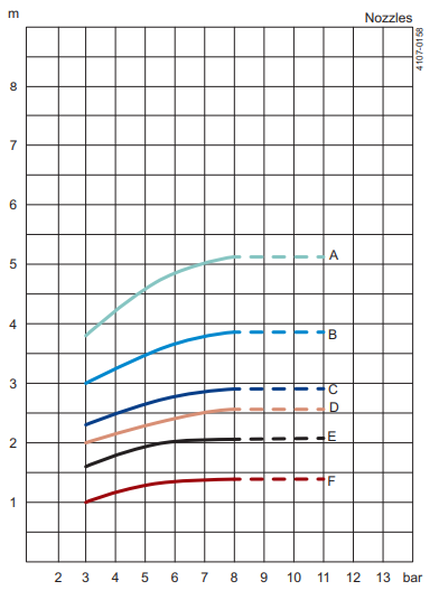 |
|
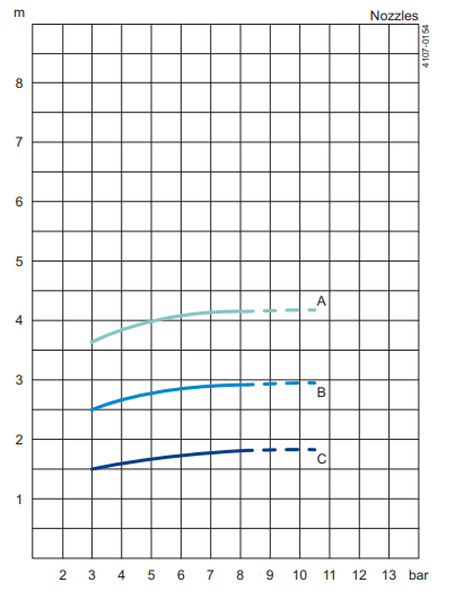 |
|
Inlet pressure |
|
Inlet pressure |
|
A = 4 x Ø4.2 mm
B = 2 x Ø3.8 mm LS
C = 2 x Ø2.0 mm |
|
D = (5 rpm) 2 x Ø2.0 mm
E = (16 rpm) 2 x Ø3.8 mm
F = (16 rpm) 2 x Ø2.0 mm |
|
|
A = 4 x Ø4.2 mm
B = 2 x Ø3.8 mm LS
C = 2 x Ø2.0 mm |
|
|
Dimensions (mm)
|
Media Driven
|
.png) |
A |
B |
C |
D |
E |
F |
G |
H |
I |
J |
K |
537 - 687 - 887 - 1187 - 1387 - 1687 |
31 |
350 - 500 - 700 - 1000 - 1200 - 1500 |
157.25 |
132 |
172 |
Ø119 |
Ø69 |
112.5 |
23 |
Ø119 |
|
|
Dimensions (mm)
|
Media Driven
|
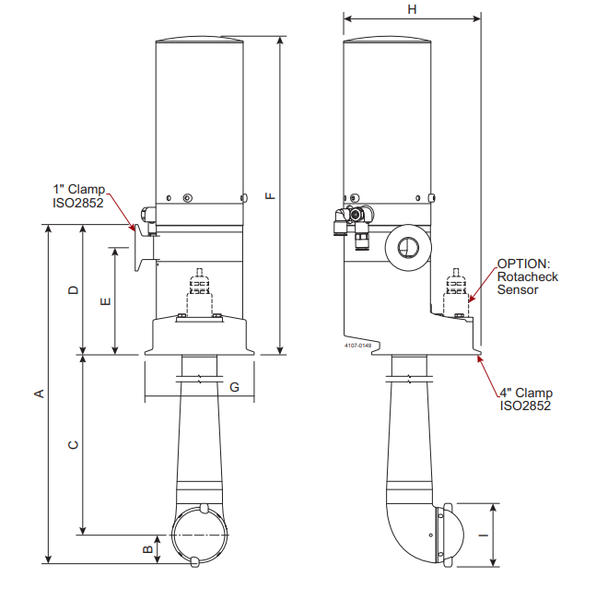 |
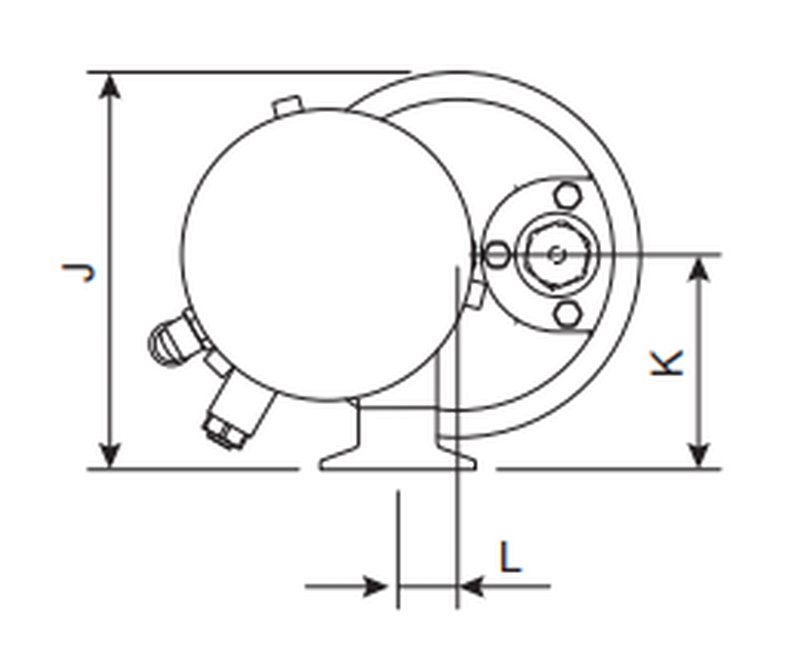 |
A |
B |
C |
D |
E |
F |
G |
H |
I |
J |
K |
L |
523 - 673 - 873 - 1173 - 1376 - 1673 |
31 |
360 - 500 - 700 - 1000 - 1200 - 1500 |
142 |
117 |
340 |
Ø119 |
168 |
Ø69 |
130 |
70 |
19.5 |
|
|
TRAX simulation tool
|
TRAX is a unique software that simulates how the Toftejorg SaniJet 20 performs in a specific tank or vessel. The simulation gives information on wetting intensity, pattern mesh width and cleaning jet velocity. This information is used to determine the best location of the tank cleaning machine and the correct combination of flow, time and pressure to implement. A TRAX demo containing different cleaning simulations covering a variety of applications can be used as reference and documentation for tank cleaning applications. A TRAX simulation is free and available upon request. |
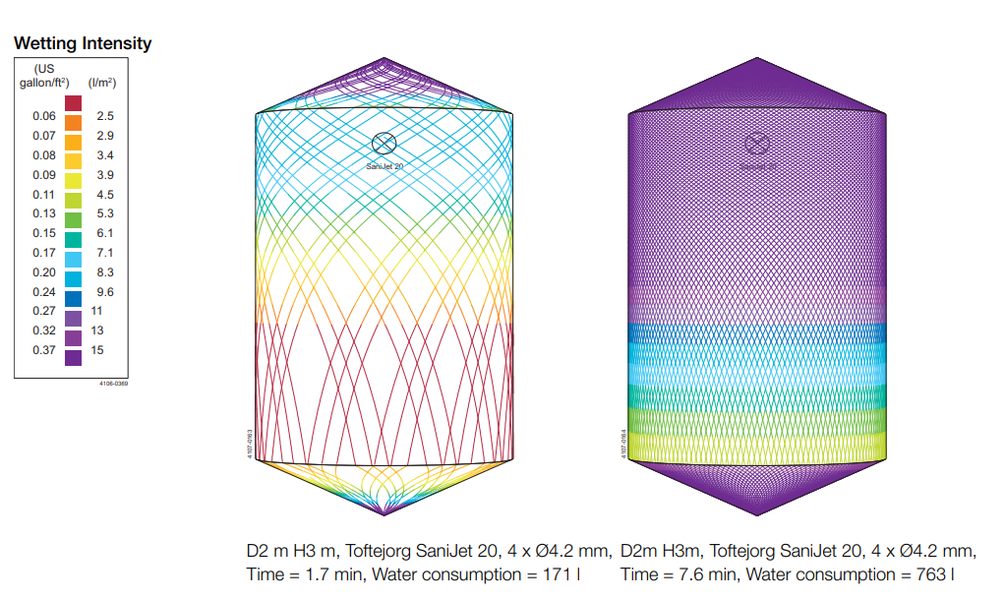 |
Cleaning Pattern, the Golden Section
|
Toftejorg SaniJet 20 operates according to the patented Golden Section cleaning pattern (EP-Patent No.: 0495883, US-Patent No.: 5,279,675), which is unique in building up a uniform pattern. The pattern starts very coarse and refines itself in a step-less way by laying out the tracks approximately in the middle of the two most distant tracks already made. This means that the jets always clean the areas containing the most remaining product, and thereby remove as much deposit as possible in the shortest possible time. In some instances, this method of cleaning can even render a complete cleaning pattern unnecessary. The Golden Section is the most suitable cleaning pattern for an effective pre-rinse. |
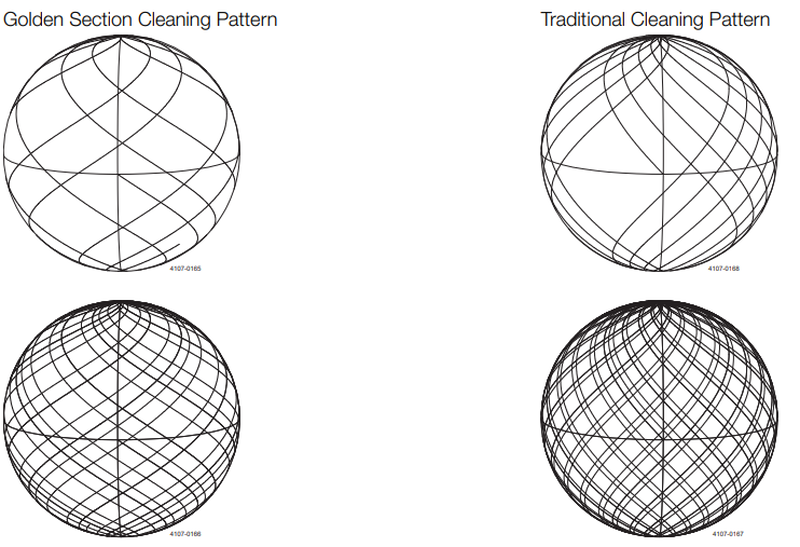 |
|