Introduction
|
The Alfa Laval MultiJet 45 is a rotary jet head tank cleaning machines for use in industrial environments. Built to clean tanks with capacities up to 500 m3 it combines pressure and flow to create high-impact cleaning jets that rotate in a repeatable and reliable 360- degree cleaning pattern |
The MultiJet 45 minimizes the consumption of water, and cleaning media. Easy to customize to meet customer requirements, it allows companies to spend less time cleaning and more time producing. |
|
Application
|
The Alfa Laval MultiJet 45 is designed for the removal of the toughest residues from industrial tanks across a broad range of industries, such as the chemical, pulp and paper, ethanol, starch, oil. |
|
Benefits
|
- 60% faster cleaning = more time for production
- Saves up to 70% of your cleaning cost
- Eliminates the need for confined space entry for manual tank cleaning
- Allows re-circulation of CIP media with particles in, up to 3 mm particle size
- Robust and durable design
|
|
Standard Design
|
The choice of nozzle diameters can optimize jet impact length and flow rate at the desired pressure. A 2.1 material certificate and an ATEX certification are available. |
Alfa Laval offers a wide range of tank cleaning machines suitable for different duties and industries. An alternative that offers performance similar to the Alfa Laval MultiJet 45 is the Alfa Laval GJ 8 for applications that require a small tank inlet opening. |
The above drawings show the cleaning pattern achieved on a cylindrical horizontal vessel. The difference between the first cycle and the full pattern represents the number of additional cycles available to increase the density of the cleaning. |
|
Working principle
|
The high-impact jet stream from the Alfa Laval MultiJet 45 rotary jet head covers the entire surface 360° of the tank interior in a successively denser pattern. This achieves a powerful mechanical impact with a low volume of water and cleaning media. |
The flow of the cleaning fluid makes the nozzles perform a geared rotation around the vertical and horizontal axes. In the first cycle, the nozzles lay out a course pattern on the tank surface. The subsequent cycles gradually make the pattern denser until at full cleaning pattern is reached. |
Once the full cleaning pattern is reached, the machine will start over again and continue to perform the next full cleaning pattern. |
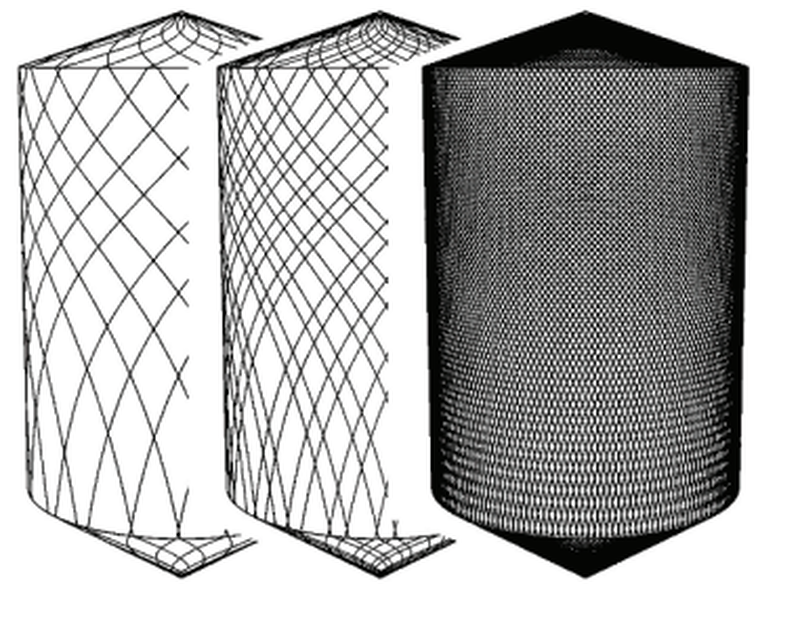 |
|
Certificates
|
2.1 material certificate and ATEX. |
|
|
|
|
TECHNICAL DATA
|
|
|
|
Lubricant |
Self-lubricating with the cleaning fluid |
Max. throw length: |
4 nozzle: 8 - 17 m |
Impact throw length: |
4 nozzles: 4 - 10 m |
|
|
Pressure |
|
Working pressure: |
4 nozzles: 3 - 12 bar |
Recommended pressure: |
4 nozzles: 5 - 6.5 bar |
|
|
PHYSICAL DATA
|
|
Materials |
316L (UNS S31603), PTFE, PEEK, ETFE, FPM, TFM |
|
|
Surface finish |
|
Exterior finish: |
Mat |
|
|
Temperature |
|
Max. working temperature: |
95°C |
Max. ambient temperature: |
140°C |
|
|
|
|
Weight: |
4 nozzles: 6.1 kg |
|
|
Connections |
|
Standard female thread: |
1½"Rp (BSP) male, 1½" NPT male, adapter connection |
|
|
Caution
|
Avoid hydraulic shock, hard and abrasive particles above 3 mm in the cleaning liquid, as this can cause increased wear and/or damage of internal mechanisms. In general, a filter in the supply line is recommended. Do not use for gas evacuation or air dispersion. For steaming we refer to the manual. |
|
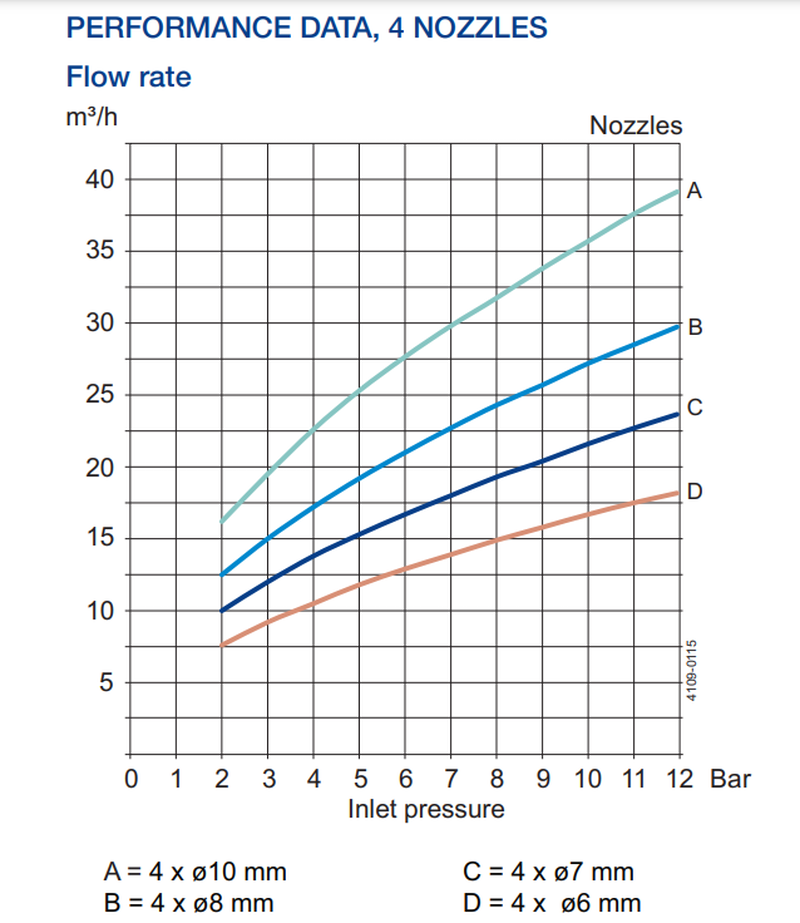 |
|
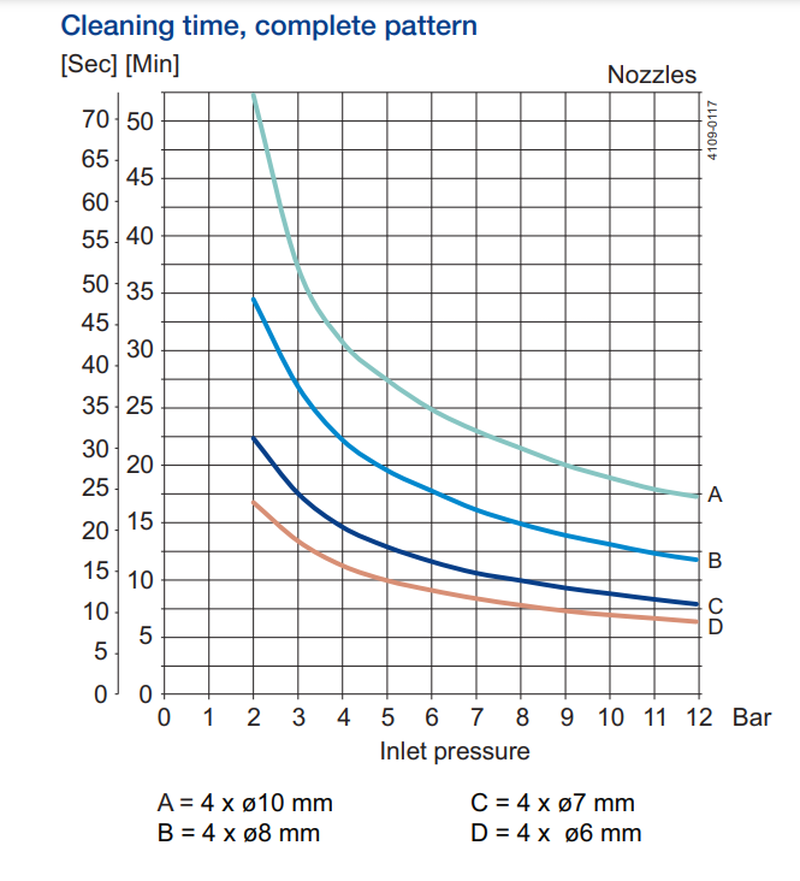 |
|
|
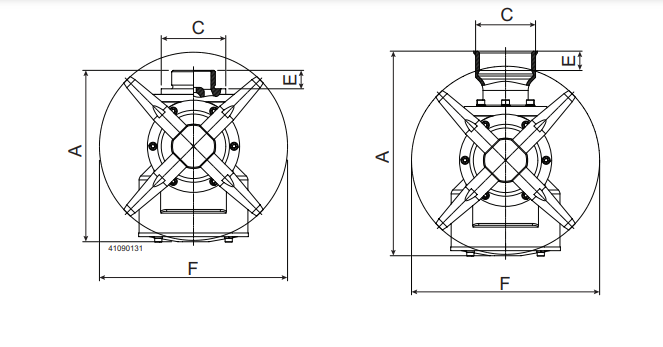 |
Thread (1½” Rp) male or Thread (1½” NPT) male
|
|
Female connection, prepared for adapter
|
|
A |
C |
E |
F |
mm |
222 |
222 |
21 |
204 |
|
|
|
Qualification Documentation
|
Documentation specification |
|
ATEX |
ATEX approved machine for use in explosive atmospheres
Catagory 1 for installation in zone 0/20 in accordance with Directive 2014/34/EU
II 1G Ex h IIC 85 °C ... 175 °C Ga
II 1D Ex h IIIC T85 °C ... T140 °C Da |
|