Introduction
|
The Alfa Laval SaniJet 25 UltraPure is a rotary jet head tank cleaning machine for hygienic environments. Built to clean tanks with capacities from 15-150 m3 it combines pressure and flow to create high-impact cleaning jets that rotate in a repeatable and reliable 360-degree cleaning pattern. |
The SaniJet 25 UltraPure minimizes the consumption of water, and cleaning media. Easy to customize to meet customer requirements, it allows companies to spend less time cleaning and more time producing. |
Alfa Laval UltraPure equipment is designed and configured to meet the high demands of the biotech and pharmaceutical industry. Special attention is given to documentation, material and surface finish, in compliance with current Good Manufacturing Practices (cGMP) and other guidance for this industry. |
|
Application
|
The Alfa Laval SaniJet 25 UltraPure is designed for the removal of the toughest residues from hygienic tanks across a broad range of industries, such as the pharmaceutical and personal care industries. |
|
Benefits
|
- 60% faster cleaning = more time for production
- Saves up to 70% of your cleaning cost
- Eliminates the need for confined space entry for manual tank cleaning
- High-impact cleaning in a 360° repeatable cleaning pattern
- Cleaning process can be validated using Alfa Laval Rotacheck
- Alfa Laval Q-doc documentation package
|
|
Standard Design
|
The choice of nozzle diameters can optimize jet impact length and flow rate at the desired pressure. |
|
Working principle
|
The high-impact jet stream from the Alfa Laval SaniJet 25 UltraPure rotary jet head is designed to cover the entire surface of the tank interior in a successively denser pattern. This achieves a powerful mechanical impact with a low volume of water and cleaning media. |
The flow of the cleaning fluid makes the nozzles perform a geared rotation around the vertical and horizontal axes. |
In the first cycle, the nozzles lay out a course pattern on the tank surface. The subsequent cycles gradually make the pattern denser until at full cleaning pattern is reached. Once the full cleaning pattern is reached, the machine will start over again and continue to perform the next full cleaning pattern |
|
Cleaning Pattern
|
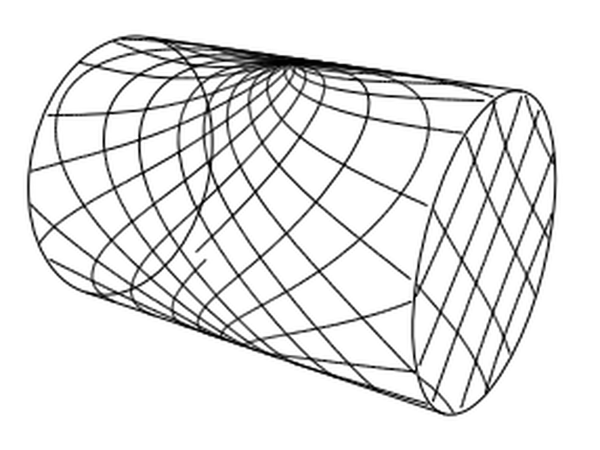 |
|
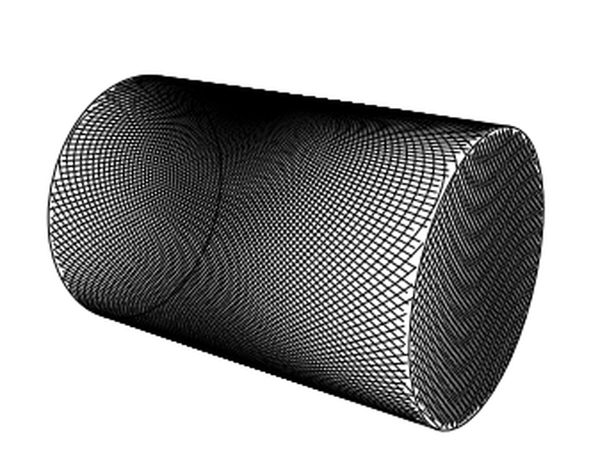 |
First cycle |
|
Full pattern |
|
|
The above drawings show the cleaning pattern achieved on a cylindrical horizontal vessel. The difference between the first cycle and the full pattern represents the number of additional cycles available to increase the density of the cleaning. |
|
Certificates
|
Q-doc, Q-doc incl. FAT/SAT and ATEX |
 |
|
TECHNICAL DATA
|
|
Lubricant |
Self-lubricating with the cleaning fluid |
Standard Surface finish: |
Ra 0.5µm exterior / Ra 0.8µm internal |
Max throw length: |
12.5 - 17 m |
Impact throw length: |
5.5 - 10m |
|
|
Pressure |
|
Working pressure: |
3 - 8 bar |
Recommended pressure: |
5 - 6.5 bar |
|
|
PHYSICAL DATA
|
|
Materials |
316L (UNS S31603), Duplex steel (UNS N31803), Duplex steel (UNS S21800), PEEK*, PFA* and EPDM* |
* FDA compliance 21CFR§177 |
|
|
Welding connection |
1" ISO, 1" ANSI/Sch40, 1½" BPE US/SWG, 1½"Dairy, 1½"ANSI/Sch40 or NW40. |
|
|
Temperature |
|
Max. working temperature: |
95°C |
Max. ambient temperature: |
140°C |
|
|
|
|
Options
|
Declaration of Conformity with ATEX approved, Category 1 for installation in zone 0/20. |
|
Caution
|
Avoid hydraulic shock, hard and abrasive particles in the cleaning liquid, as this can cause increased wear and/or damage of internal mechanisms.In general, a filter in the supply line is recommended. Do not use for gas evacuation or air dispersion. For steaming we refer to the manual. |